The customer is a global first-class supplier in the automotive industry and is famous for R & D and manufacturing transmission systems.

Modern intelligent gear shaft hardness test needs to improve process standards and simplify operator influence. With soft turning and cutting operations, the shafts and gears in the transmission system are subject to furnace heat treatment, surface quenching and hardening. In case hardening, the surface layer of the component is first enriched with carbon and then hardened. This increases the hardness of the surface layer, thereby increasing the compressive and fatigue strength, as well as wear resistance. The core of the sample maintains toughness and has high strength, so the impact resistance is the basic feature of the transmission system. Tempering is performed as part of the hardening process. Tempering slightly reduces the hardness, The yield strength is greatly improved (toughness). For fast and simple quality and process control, each batch of parts must be tested immediately after the heat treatment process. At the same time, it is required to improve the process standard. The classification of this batch must be called at any time in the future, and all relevant data must be saved automatically. The modern intelligent gear shaft hardness tester meets the following requirements: 1. A variety of parts, according to Production line: various shapes and sizes need to be tested. 2. Operation process speed: scan the bar code of parts, and the hardness tester retrieves the test method from the database and returns the test results. 3. Simplify user operation: QA software assigns test pieces and transmits test results to QA software through RS232 interface. 4. The hardness tester is easy to operate: multiple operators conduct hardness tests on multiple production lines without complex training. 5. Light and compact: due to the space limitation of the hardening workshop, the hardness tester should not occupy a large space. Solution durajet10g5 simple, fast, modern and intelligent gear shaft hardness test a durajet10 is placed in each production line. Since the main load of the electronic ballast control system is from 1 to 250kgf, a single equipment can cover the whole Rockwell range. The surface hardness can be measured directly and quickly on the production line. In addition, the durajet of 300x740x565mm is a compact and lightweight hardness tester. Therefore, it does not require much space. Due to the high precision test head, a wide range of components can be clamped and tested. Use serial interface (RS232) can carry out complete data management. All data are input and output in ASCII format. Therefore, all data can be exported to the company's QA software for further processing. Therefore, the data will not be lost. Why choose us? Machine friendliness is particularly important for the production team leader. All employees in the hardening workshop should be able to work without much training Operate the machine with practice. Durajet implements this standard. The software developed by emco-test can be operated simply by using fingers or stylus through a clear, backlit touch screen. 'We have been cooperating with EMCO test and are satisfied with their cooperation. In my opinion, they are the pioneers of today's hardness tester technology. I can't find a durajet like hardness tester from other suppliers in the market. The electric clamping function of parts is accurate. I also like this design. Compared with other suppliers, this equipment has the best internal technology, but from the perspective of appearance design To keep a low profile. '
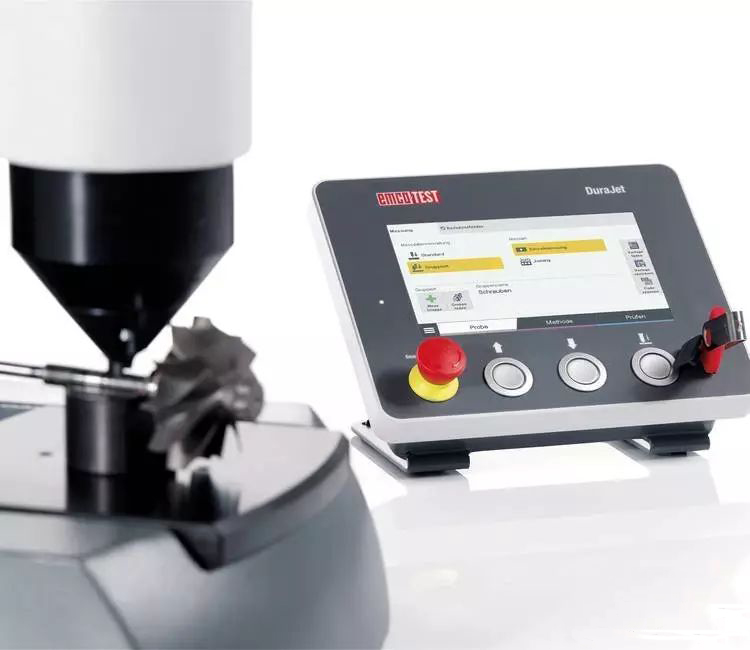
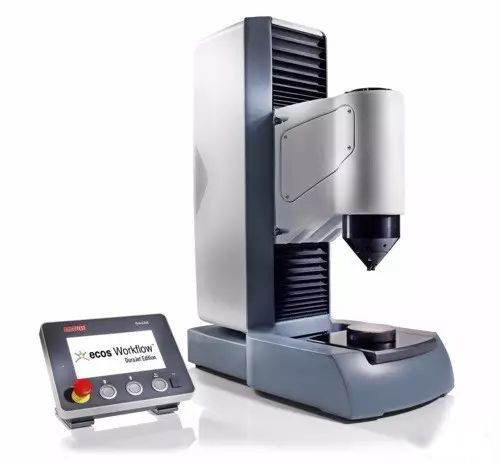